
Introduction
In this blog post, we will take a look into the
planning with characteristics process within Advanced Planning using the SAP S/4HANA Manufacturing for planning and scheduling capability of
SAP Digital Supply Chain Management, edition for SAP S/4HANA (DSC Edition).
We will refer to this solution as DSC Edition in this blog for brevity.
The DSC Edition provides advanced production planning and detailed scheduling (PP/DS) capabilities through the SAP S/4HANA Manufacturing solution for planning and scheduling.
The solution’s production planning capabilities match overall supply to demand. With access to global supply and demand data, you can use multiple planning tools to resolve typical plant level conflicts and arrive at an optimized, executable plan for detailed scheduling.
Detailed scheduling capabilities use the executable production plan to derive the optimal sequence of activities required to meet specific production commitments that can be released to the shop floor for execution.
In this post, we will also point to the
Implementation Guide for SAP S/4HANA Manufacturing for Planning & Scheduling 2022 frequently and will refer to it as, simply, the Implementation Guide.
Business Scenario
To focus on the influence of
characteristics on the planning process, we will simplify our Bill of Material (BOM) and task list. We will cover an example where we manufacture a packet of tissue paper sheets (finished material) out of pulp (semi-finished material) in a Make-to-Stock (MTS) scenario.
The tissue paper packet has fixed dimensions and fixed number of sheets. It is available in various ply options (number of layers) from 1 Ply to 3 Ply, and in 3 different colors - white (uncolored), tan and pink. Both, the ply and color, can be configured during the creation of the sales order.
In our scenario, usually, we have enough stock for different configurations of the tissue paper, example: 2 ply in Tan color, 3 ply in Pink color, etc. The sales orders are usually fulfilled from the available stock.
When we run production planning for the tissue paper, planned orders will be created to cover the sales orders (demand) in case of shortages. These planned orders have the same characteristic values as the demands they cover. The pulp color and quantity required to manufacture the tissue paper depend on the ply and color (and quantity) of the tissue paper in the planned order (and, in turn, sales order).
We do not plan or cover the pulp shortages on-the-fly. Hence, in case we do not have enough quantity of pulp for the required color, the planning for the tissue paper would simply fail.
Pre-requisites
This post assumes that:
- The sections 2 and 3 of the Implementation Guide are already maintained in your SAP ERP and DSC Edition systems.
We will look into a few of the sub-sections again in this post.
- If you use SAP ECC as your ERP system, you have at least one customer in your ERP system and you have transferred this customer to the DSC Edition system using ALE integration. If you use SAP S/4HANA as your ERP system, you have at least one Business Partner with customer role in your ERP system and you have transferred this BP to the DSC Edition system using DRF integration.
You have created location of type Business Partner in the DSC Edition system.
Refer the sections 7.2 and 4.1.7 of the Implementation Guide for more details.
- In your DSC Edition system, you have maintained a mapping between the S/4 fields STPO-MENGE and PP/DS field /SAPAPO/CULL_CFG_COMPONENT-QUANT in the Object Characteristics Mapping table /SAPAPO/CUCDPMAP.
Customizing setup
We will use an Organizational Area "Z" for our example. This Organizational Area is defined for class types 023 and 300 and is maintained in the ERP system as well as the DSC Edition system.
An Integration Model is also created, generated and activated for this Organizational Area with destination as the DSC Edition system in both the systems.
Refer the sections 3.1.6, 3.2.7, 7.1.1 and 7.1.2 in the Implementation Guide for more details on the CIF transfer of Classes and Characteristics.
The configuration schema of the DSC Edition system (section 3.2.8 in the Implementation Guide) has been set to Characteristic-Dependent Planning (CDP).
Note: This example will also work if the configuration schema has been set to Variant Configuration (VC).
Master Data setup
Material independent master data
As per our Business Scenario, we model our tissue paper and pulp properties using characteristics.
In the ERP system, we will create the following characteristics:
- TP_COLOR with 3 colors - PNK (Pink), TAN (Tan) with White/Uncolored as default

- TP_PLY with 3 allowed values - 1, 2 and 3

- a Reference Characteristic PULP_QUANTITY with reference to STPO-MENGE field to influence the component quantity of the pulp during BOM and PDS explosion.

Using Organizational Area "Z" and class types 023 and 300, we will create class TP including TP_COLOR and TP_PLY as the characteristics and class PULP including TP_COLOR as the only characteristic. We will create 4 classes in total.

Batch Class for Tissue Paper

Variant Class for Tissue Paper

Batch Class for Pulp

Variant Class for Pulp
Material dependent master data

Master Data setup
We will create the materials and work center as per the
Master Data setup image above. We will also create configuration profiles for both the configurable materials. We will also create the BOM as per the above image and create one object dependency of type "Procedure" to influence the component quantity of the pulp based on the ply of the tissue paper as below. This object dependency result will override the static quantity maintained at the BOM item (component) level.
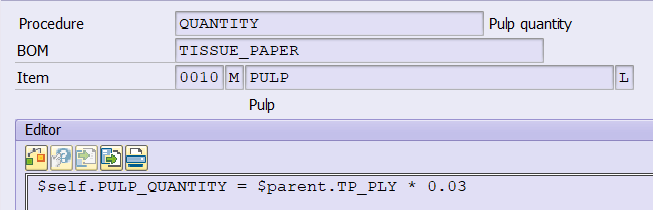
This formula defines that 30 grams (0.03 KG) of pulp is required per ply of tissue paper. So, for 1 unit of a 2 ply paper, the component quantity of pulp would be 0.06 KG (60 grams).
Note: The constant of 0.03 is assumed to have been derived from the GSM property of the paper.
The routing and production version will also be created as per the
Master Data setup image.
For the pulp, 3 batches with classification will be created and stock will be added to each of the batches as below:
Batch |
TP_COLOR value |
Stock Quantity (KG) |
---|
PNK_PULP |
PNK |
5 |
TAN_PULP |
TAN |
8 |
UNC_PULP |
<empty> |
10 |
Note: If your ERP system is an SAP ECC system, you would need to maintain the Planning Procedure for your Pulp component in the DSC Edition system after the CIF transfer.
Integration with DSC Edition system
In the ERP system. once all the master data is setup, we will create integration models with the DSC Edition system as the destination for the following CIF objects:
- Work Centers
- Classes/Characteristics with Org Area = 'Z' and additional characteristic as PULP_QUANTITY
- Materials with Activate Planning = 'A'
- PDS (ERP)
- Storage Location Stock
- Sales Orders
- Planned Orders
- Batches
Next, we will generate and activate the integration models.
If your DSC Edition system has CDP as the configuration schema, verify that the classes TP and PULP with class type 400 are now available in your DSC Edition system.
Note: If your DSC Edition system is lower than SAP S/4HANA 2022, you will need to transfer the characteristics and classes using ALE integration prior to the creation of Integration Models (please refer the section 7.1 of the
Implementation Guide for SAP S/4HANA Manufacturing for Planning & Scheduling 2021 for more details).
Planning Process
Scenario 1
We will start our example by creating a Sales order in our ERP system for our finished material. We will request 100 quantities of 2 Ply Tissue Paper with Pink Color. On save, this Sales Order will get transferred to the DSC Edition system and we can view it in Product View (T-code: /SAPAPO/RRP3).

We will now run the Product Heuristic (SAP_PP_002) in Product View for this shortage situation. We see that the Planning has failed, and no Planned Order was created.
This is because, based on our object dependency, we would have needed 6 KG (100 demand x 2 Ply x 0.03) of Pink Pulp for a successful planning run. However, since our batch PNK_PULP has only 5 KG in stock, and since we cannot procure/produce the shortage of 1 KG (Planning Procedure = 1), our planning run failed as expected.
Scenario 2
We will now go back to our Sales Order in the ERP system. We will change the configuration of our Tissue Paper to 3 Ply Uncolored and save. We can verify these changes in Product View.

We will run the Product Heuristic again and see that a Planned Order gets created for quantity 100 with the same configuration as the Sales Order.

This Planned Order has a requirement of 9 KG (100 quantity x 3 Ply x 0.03) of Uncolored Pulp. Since our batch UNC_PULP has 10 KG in stock, this requirement can be fulfilled, and the planning was successful. You can see that the Surplus of UNC_PULP as 1 as 9 KG was consumed by the demand.
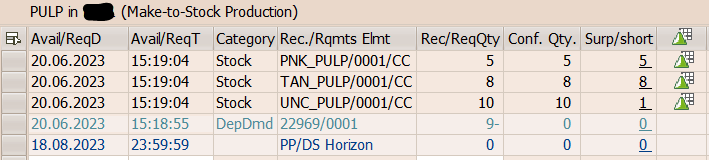
The pegging structure is as below:

Observation
The color of the pulp (component) demand is derived from the color of the tissue paper (header) planned order during the planning run without any need for an explicit object dependency, as both the materials are configurable materials.
The quantity of the pulp (component) demand is determined dynamically based on the tissue paper characteristics, the object dependency maintained in the ERP system, and the Object Characteristics Mapping maintained in the DSC Edition system.
Planning Procedure of 1 (Manual with Check) for the pulp (component) ensured that the planning for the tissue paper (header) fails if enough quantity is not available for the component.
Conclusion
To summarize, in this post, we took a look into a subset of features available under
Planning with Characteristics functionality of PP/DS in a side-by-side setup with DSC Edition. We looked into the recommendations and instructions under different sections of the Implementation Guide. We used those to build an end-to-end scenario for running production planning using characteristics in the DSC Edition system.